A Complete 6-Step Guide to Maintenance of Plate Rolling Machine
- Rohan Shah
- May 8, 2023
- 5 min read
Updated: Dec 22, 2023
Do you have a plate rolling machine at your workshop? If yes, you may already know how crucial the maintenance of such a machine is. Maintaining your machine doesn’t only benefit its life expectancy but also maintains the quality of work. A thing to keep in mind is that you should hire a machine operator who knows the plate rolling machine inside out. The workshops put their machines through heavy workloads and, ignoring the maintenance, learn the difficulty of why maintenance of a plate rolling machine is vital.
If you own a business, you would already know how costly plate rolling machines are and how crucial it is to maintain their maximum workload capacity. If you’re wondering how to perform maintenance of a plate rolling machine, take a diary and pen, and jot down these 6 steps of machine maintenance.
Step 1: Inspecting the Plate Rolling Machine
The plate bending process involves using lubricants, residue post-rolling, and cut-down or broken parts of the steel plate that you would have rolled earlier.
Let us tell you about the different parts of a plate rolling machine first.
Parts of a Plate Rolling Machine
Bearings: Support moving parts of the machine. Decrease friction.
Gears and Shafts: They transmit power and motion to different areas of the machine.
Rollers: Form and shape metal plates as they are fed to the machine.
Frame: It is the body of the machine.
Hydraulic Systems: They control the rotation of rollers at varying speeds and pressure to obtain required angles through the rolling job.
Electronics and Electrical Systems: Transmits power and allows the operator to control the machine using the console.
Plate Feeding and Handling System: Component that loads and feeds the metal plates to the rolls of the machine.
Lubrication system: Lubricates the machine for minimum friction and a smooth work process.
Before you commence the work during your shift, you must clean the machine and look for residue or broken parts. Also, check the state of the rolls of the machine. Follow these sub-steps to perform your daily inspection.
Turn off the plate rolling machine before the inspection.
Inspect the machine and look for the residue from the previous shift or day.
Check for abnormalities on different parts of the machine
Make sure the tightening screw is, well, tight.
Inspect the brakes and ensure they are set at normal to be reliable.
You must have realized that you should do this basic inspection every day before starting the work shift. It sounds like a very basic daily cleanliness routine, and it is. However, when you have bigger fish to fry, it is necessary to make sure the basic cleaning procedures are followed. Now you can move on to precautions that you must take to maintain your plate rolling machine.
Step 2: Precautionary Protocols for Maintenance of Plate Rolling Machine
We all put aside the manuals that come with the machine, or the first operator would have read it. What’s necessary is to notice that the new operator must have learned things from the old one. They might not know about tiny details and the warnings and advice about cleaning the machine.
Efficient cleaning requires you to strictly follow the guidelines from the machine manual. Here are the five instructions you should know and follow during the maintenance of the plate roller machine.
I) Don’t use solvents or inflammable materials. They may cause direct harm to the machine.
II) Make sure the grease doesn’t disperse in the air.
III) Restore guards after cleaning them with metal cleaner or polish. Do not forget to fit the guards again. Deactivated guards increase the chances of injuries.
By far, what we have discussed are routine and basic cleaning and maintenance procedures. Next up, how to perform a detailed inspection before starting the work.
Step 3: Detailed Inspection Before Rolling the Plate
Check for all the parts to be in working order. Note if there are any deformities or refrain from using if any critical parts are missing, broken, or deformed.
I) Inspect external parts of the machine for deformity or damage.
II) Set indicator lights to normal and check operation switch, limit position, and console.
III) Check pipes and tubes for leaks. It includes checking oil pumps and cylinders and
IV) Ensure the rollers are working properly and the brakes are in shape.
V) Ensure the pressure gauge is working properly.
VI) Lubricate parts that require manual lubrication.
Daily After-Work Maintenance
Leave the machine in better condition than you found it while starting your shift. This will automatically inspire the next shift operator to perform regular maintenance as you do every day.
I) Check the normal operation of the safety device
II) Ensure proper working of braking mechanisms
III) Remove all the residue from the post-rolling process using a dry cloth. Use industry-standard neoprene or PVC gloves.
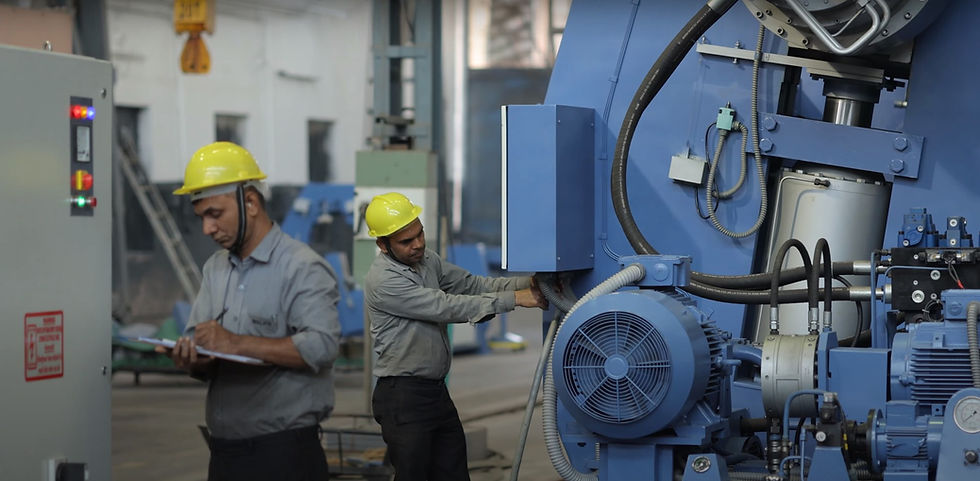
Step 4: Weekly Maintenance of the Plate Rolling Machine
This inspection is crucial as the filters might or might not get filled after a week. So here’s what you need to do.
I) Check for the proper functioning of the emergency stop mechanism
II) Inspect side protectors
III) Check for the proper functioning of the rear protector
IV) Filter has an indicator that tells you whether it is clogged. Unfortunately, the yellow indicator light on the vacuum switch means you must replace the filter immediately.
Step 5: Monthly Maintenance of the Plate Rolling Machine
You don’t want the machine to have leakages and month-old residue in the finer areas where it is impossible to reach every day because it takes time. Performing monthly maintenance keeps your machine in check for the standard.
I) Clean all pipes, tubes, and hydraulic components:
Cylinders, valves, motor/pump units, and other pipe and tubular systems.
It helps you make sure there are no leaks
This way, the contaminants cannot get into the machine while removing and replacing components
II) Check all the internal and external fittings and ensure no leaks or loose fittings.
III) Have flexible tubing that connects the pump and system. Upon swelling, replace right away.
IV) Check the oil level, for it is necessary to maintain energy transmission, conversion and control over the machine.
V) Tank air filter should be cleaned with compressed air.
Step 6: Annual Maintenance of the Plate Rolling Machine
Machine parts that take time to wear down or some filters that get filled slowly over time must be checked annually.
I) Upon the pressure drop reaching 1 bar, you should change the oil separator microfilter. Or, do it anyway after a year. It is a beneficial measure to take.
II) Re-fill oil in the hydraulic circuit
III) Replace the oil filter element with a new one.
Final Touch
A plate rolling machine is a heavy investment for any size of business. It is not a miscellaneous expense. Even after knowing this, some workshops continue overloading their plate rolling machines and neglect regular, weekly, monthly, or annual inspections. Take a pen, not these steps, and start working with due diligence. We at Himalaya Machinery provide the best plate rolling and straightening solutions. Contact us through the mail and share your requirements with us.
Comments